Forced Circulation Evaporators
Engineering and Manufacturing Evaporators for Chemical Process Industries
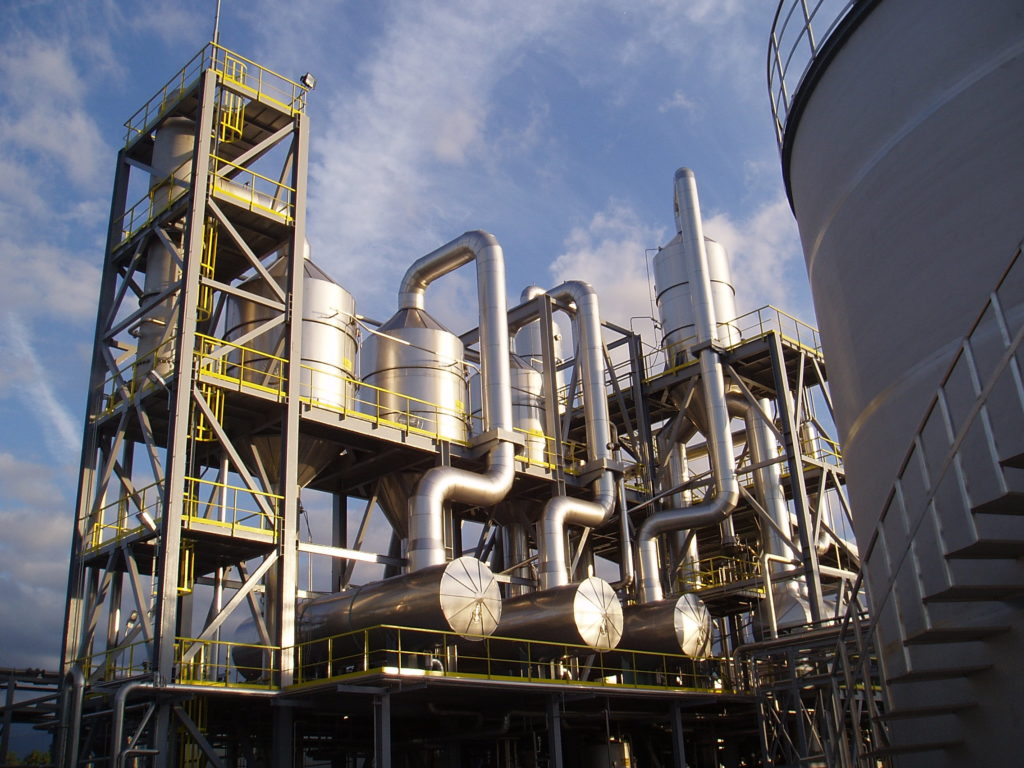
Forced Circulation Evaporators
As the name implies, liquor in a forced circulation evaporator is pumped through the tubes to minimize tube scaling or salting when precipitates are formed during evaporation. A Swenson forced circulation evaporator (with a submerged inlet) complete with a single-pass vertical heat exchanger, elutriating leg, cyclone, and top-mounted barometric condenser is shown in the photo.
Slurry is pumped from the bottom cone of the vapour body through the tubes of the vertical heat exchanger, where heat is added, and back into the vapour body where evaporation occurs. Sufficient slurry height (submergence) is maintained above the tangential inlet on the vapour body and above the top tubesheet of the heat exchanger to suppress mass boiling in the inlet and prevent surface (local) boiling on the tube surface. This is necessary to preclude salt precipitation on the tangential inlet and tubes.
A high circulation rate is provided for adequate tube velocity to achieve good heat transfer. Therefore, lower slurry temperature rises are assured which minimize supersaturation of the solution.
A sufficient quantity of salt crystals is suspended in the circulating system to provide seed crystals in the boiling zone for salt growth. Adherence to these basic principles of crystallization results in coarse crystals and minimal wall and tube salting, so less equipment washing is required. This conserves energy because less steam is required to boil wash water and this increases on-stream time for the evaporator.The circulating pump is usually of the axial-flow, single-elbow design, well-suited for the high flow rates and low pressure drops in Swenson designed circulating systems. These heavy duty pumps operate at low speeds, which reduce maintenance and minimize mechanical attrition of the salt crystals.
The tangential inlet provides excellent mixing of slurry in the vapour body because of the circular motion it creates. Secondary vertical currents are also generated, mixing body slurry with the hotter slurry entering the vapour body to reduce the degrees of flash. This agitation minimizes salt buildup on the bottom cone of the vapour body. A swirl breaker is provided in the circulating slurry outlet.
The vapour body is conservatively designed both in diameter and height. It is important to have adequate free space above the liquor level to allow the liquor droplets entrained in the vapour leaving the boiling surface to reach equilibrium and return by gravity to the circulating slurry. Large diameters result in low upwards vapour velocities which minimize entrainment and provide adequate retention time for salt growth.
A mesh type entrainment separator may be installed in the upper portion of the vapour body to reduce solids carryover to normally less than 50 parts per million parts of vapor. Other types of entrainment separators are also available.
The elutriating leg, attached to the bottom cone of the vapour body, is a convenient device for thickening the slurry it receives from the vapour body and for salt crystal washing and classification. Slurry enters the top of the leg through a unique slurry-inlet device, which improves washing efficiency by reducing agitation in the leg. Salt crystals are fluidized and washed in the leg with a portion of the feed liquor which enters the bottom cone and is distributed with a perforated, dished head. Smaller crystals are washed into the vapour body for additional growth and the larger crystals are discharged from a connection near the bottom of the leg.
A Swenson-designed, low-pressure-drop liquid cyclone is sometimes used to clarify liquor discharged from the evaporator. The driving force is the pressure drop across the circulating pump. Thickened slurry is returned through a wide-open cyclone underflow connection to the circulating piping before the pump suction.
Another Swenson innovation is the direct-contact condenser mounted on the vapour body. A short piece of vertical pipe connects the vapour body with the condenser to minimize piping and pressure drop. This design also eliminates structural steel for support of a separate condenser.